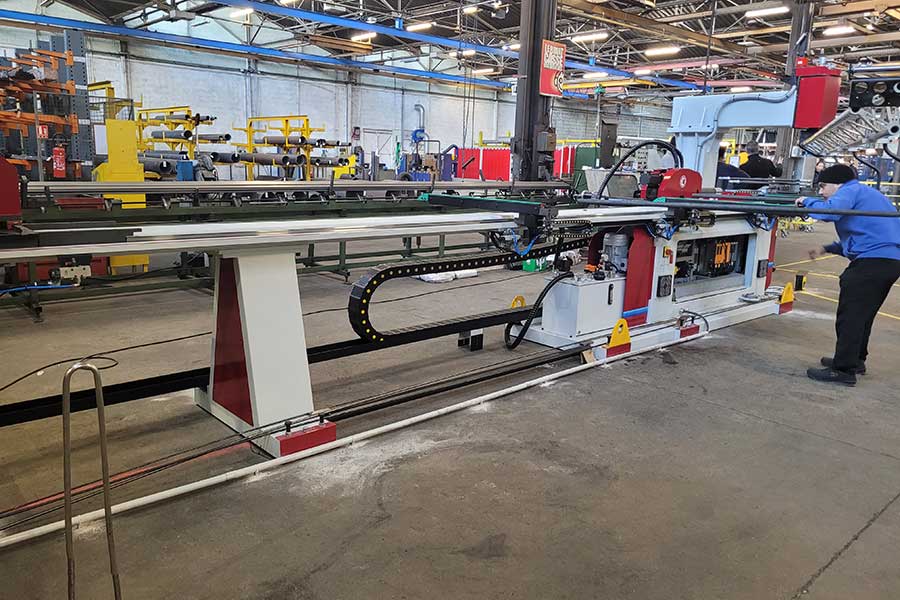
Stargroup and the shell and tube heat exchanger sector
A new EvoBend 450 tube bundle heat exchanger finds a home on French soil!
The purchasing company, which specialises in the production of shell and tube heat exchangers, identified Stargroup as the ideal partner to meet its needs. Indeed, the EvoBend 450 was chosen by the French company to replace a previous tube bender.
For Stargroup, meeting the customer's needs was a stimulating challenge: bending tubes up to 180° with a diameter between 12 mm and 19.05 mm and a length of up to 12 metres.
To meet these requirements, a tube bender was supplied with:
• standard bending equipment, consisting of a die, slide, clamp, tile and core;
• roller equipment, to obtain the compression bending and to perform the bending of the tube;
• a mobile support arm.
The arm, movable during the bending phase, will help during bending to support even the longest hairpins, which would otherwise end up bending due to the thin diameter.
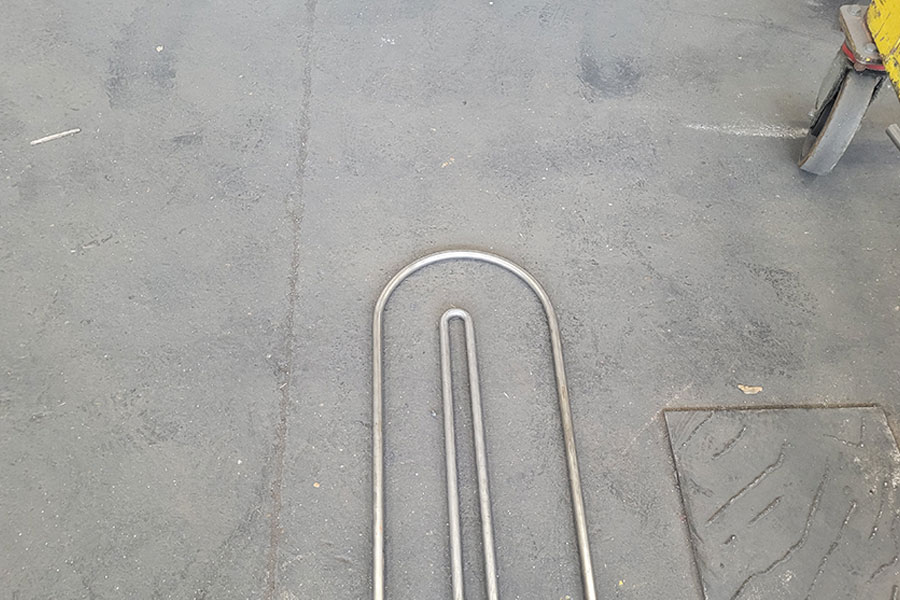
Design and function of shell and tube heat exchangers
The shell and tube heat exchanger consists of a number of tubes mounted inside a cylindrical casing. The tubes inside the casing are bent into a U-shape forming the so-called hairpin and are subsequently welded to the end plate.
Two fluids flow inside the exchanger: one fluid flows outside the tubes while the second fluid flows through the tubes.
The EvoBend series, available in sizes 250, 450, 650 and 800, is suitable for use in the bending of stainless steel tubes, guaranteeing optimum performance in the production processes of shell and tube heat exchangers.